Ensured Quality
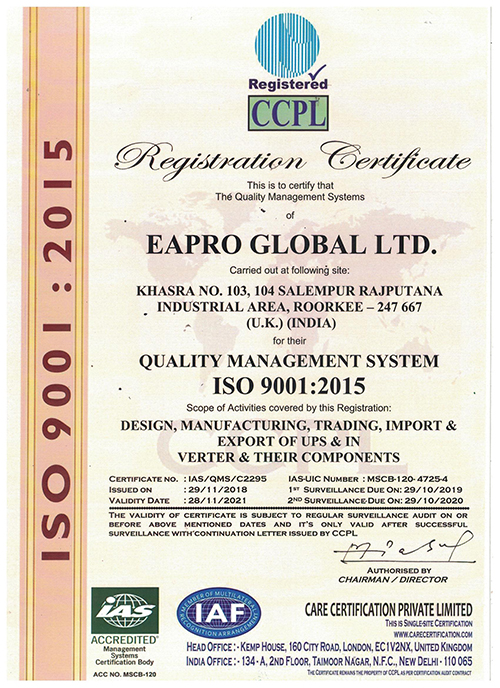
Stronger Quality Management System
The organization is committed to quality in all sphere of its activities. To ensure that its products and services are consistent and have a high degree of excellence and to provide the customer with continued satisfaction, the organization has adopted Quality Management System based on ISO – 9001 standards. Due to this, there has been visible, continual improvement in quality of product, service and various other process. As a result the organization has achieved phenomenal growth in terms of Quantity while maintaining and upgrading Quality in various activities.
Product Quality And Safety
EAPRO Global places the highest value on providing customers with reliable products. Product safety must be ensured under any circumstance, and product safety has the highest priority over sales objective, product design, and marketability and expense issues. All staff at EAPRO Global will exert their best effort to observe standards for the product safety system, acknowledging that safety is a fundamental value of products.
Quality Vision
With the strong encouragement of the Managing Director, EAPRO has reinforced to the enterprise QA organization, and is shaping the corporate culture to allow neither the slightest quality problem nor compromise on quality under the vision of EAPRO, Perceived as World Best Quality by Customers and Consumers”. EAPRO is also trying to provide consumers with the high-safety products with Zero defect by emphasis on incoming and process quality activities and quality awareness.
Incoming Quality Control
Incoming Quality Control:
- Taking samples from received lot for IQC inspection.
- Checking and verifying the inward material for its specified norms & specification.
- Ensuring good packing condition.
- Verifying the inward material with BOM, drawing & specification check sheet and as per QAP (Quality Assurance Plan ).
- Ensuring timely decision making of inwards material to prevent the production loss.
- Maintaining and updating the part inspection manual.
- Intimating to Store, Purchase, concerned Supplier for lot inspection status.
In-Process Quality Control
In-Process Quality Control:
- Verification of raw material Kit as per BOM before kit issuing to production.
- Ensuring production process of all sub assemblies.
- Ensuring proper tools & equipment are being used in production.
- Maintaining proper torque of pneumatic screw drivers.
- Ensuring skilled man power stage wise in lines.
- Updating display board as per work order & work instruction.
- Conducting calibration of testing equipment on fortnightly basis.
- Monitoring the skill of operators & providing necessary training before taking in work.
- Verification of line rejection & rejection report for Zero hrs & in-process rejection.
- Conducting process audit (stagewise) according to process check sheet & raising non conformities for correction & preventive action.
- Conduction 5”s” audit in production area.
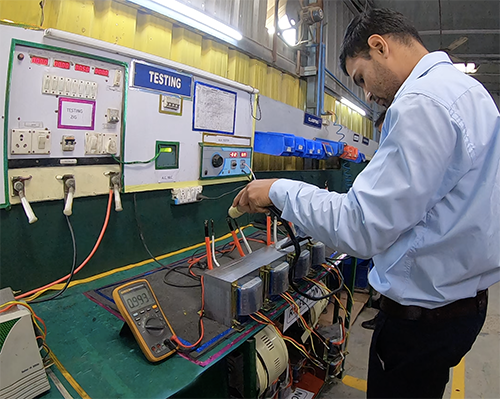
Outward Quality Control
Outward Quality Control:
- Updating and maintaining the PPAP file model wise.
- Testing of final product as per sampling plant for given specification on QA report.
- Testing & verifying the product as per work order & customer specification.
- Conducting detail inspection of two systems.
- Conducting calibration of testing equipment / jigs on fortnightly basis at OQC.
- Conducting Drop test of new model.
- Ensuring proper soaking of the system as per sampling in soaking .